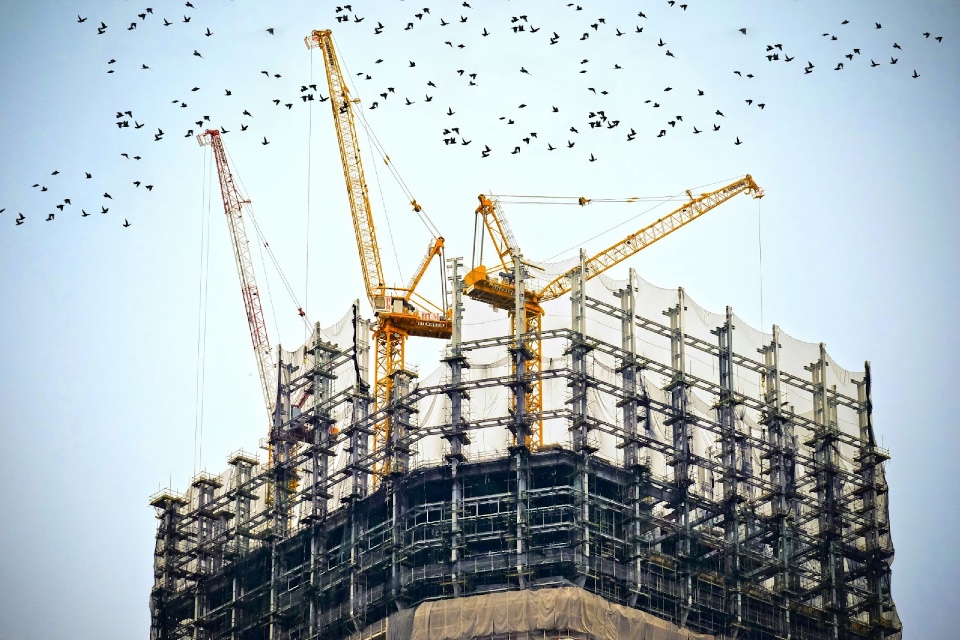
SFG20: Grenfell tragedy still looms large in public perceptions of building safety
Research conducted by SFG20 asserts that 3 in 5 people are more concerned about building safety following tragedies such as
Research conducted by SFG20 asserts that 3 in 5 people are more concerned about building safety following tragedies such as
In the UK, over 30,000 individuals experience cardiac arrests outside hospitals each year in settings such as homes, workplaces, and
By Kate Palmer, HR Advice and Consultancy Director at Peninsula Monkeypox is a rare disease that is caused by infection
One of the biggest challenges in maintaining a safe facility is information management. There are Lockout/Tagout procedures, confined space permits,
Workers looking for the lowest virus transmission risk day of the week to go into the workplace should go in
Discover BradyJet J4000 Colour Label Printer Create a safer, more efficient workplace with compliant, photo-quality full-colour labels, signs and procedures
By Coral Did you know that the most common cause of non-fatal injuries to employees is slips, trips and falls,
Winter is not the safest season. Slips & falls increase dramatically, especially when working outdoors, or simply walking to an
The countdown to Christmas has begun and, with most festivities cancelled last year, many workplaces will be looking forward to
Facilities are among companies’ most important business assets, so are you still making the most of them? Are they maximised
Businesses are being reminded of their legal obligation to ensure electrical equipment is safe to use at all times, even
The BSI is consulting on the draft Publicly Available Specification (PAS) which lays out the competence framework for individual Building
By Brady Corporation Because safety is personal. See a person instead of an object by printing a face directly on
Brady Corporation can design the optimal RFID labelling solution for asset tracking and inventory management that can fit any surface.
A very large chemicals processer increased the efficiency of asset safety inspections with inspection templates and automated reporting using reliable