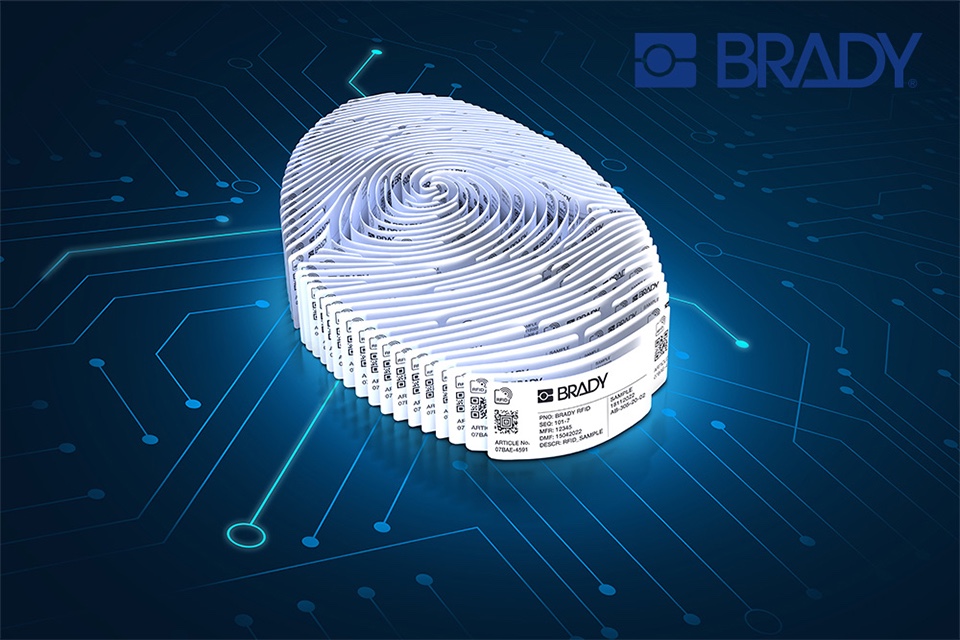
Give every asset a unique digital identity. See how!
With Brady Corporation’s complete RFID solution, assets in any industrial environment can be given unique digital identities just by applying
With Brady Corporation’s complete RFID solution, assets in any industrial environment can be given unique digital identities just by applying
One of the biggest challenges in maintaining a safe facility is information management. There are Lockout/Tagout procedures, confined space permits,
By Brady Corporation Read the case study from a cinema group, and find out how to quickly remove spills from
Discover BradyJet J4000 Colour Label Printer Create a safer, more efficient workplace with compliant, photo-quality full-colour labels, signs and procedures
…With reliable dual frequency UHF and NFC RFID labels from Brady Brady Corporation presents a new, highly reliable dual frequency
Winter is not the safest season. Slips & falls increase dramatically, especially when working outdoors, or simply walking to an
Facilities are among companies’ most important business assets, so are you still making the most of them? Are they maximised
By Brady Corporation Because safety is personal. See a person instead of an object by printing a face directly on
Brady Corporation can design the optimal RFID labelling solution for asset tracking and inventory management that can fit any surface.
A very large chemicals processer increased the efficiency of asset safety inspections with inspection templates and automated reporting using reliable
By Brady British Standard 1710-compliant, industrial-grade pipe markers that can be applied to any pipe will help you to clearly
Get acquainted with Brady Safety Management software solutions & the Brady Lockout Tagout Service offer during the short dedicated webinar.
Make safety top of mind in the workplace and optimise Lockout/Tagout efficiency with highly visible, custom lockout shadowboards. Shadowboards increase
By Brady Corporation Get experienced Brady engineers to write and implement custom Lockout/Tagout procedures for more maintenance safety. Brady engineers
Safety and identification specialist Brady Corporation offers signs for download to help stop the spread of the COVID-19 virus. Anyone