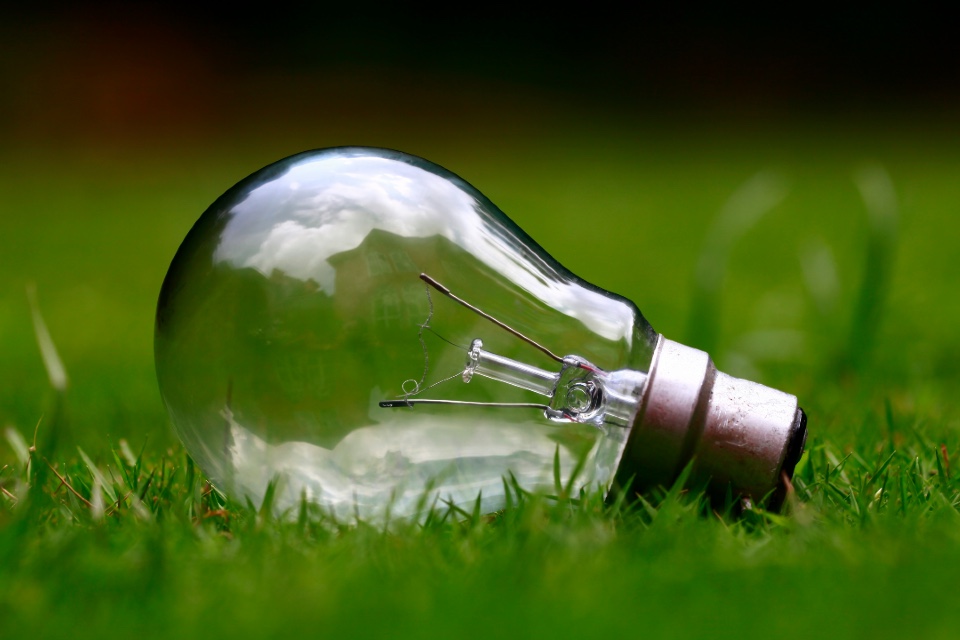
Centreco Q&A: How landlords can stay ahead of energy efficiency regulations
Asย The Timesย reported recently, more than 80 per cent of all commercial properties in England will effectively be rendered unlettable from
Asย The Timesย reported recently, more than 80 per cent of all commercial properties in England will effectively be rendered unlettable from
The road to net zero is rarely straight and for many facilities managers, itโs paved with complexity, confusion and commercial
In property and facilities management, much of the work is reactive by nature. From emergency repairs to urgent supplier payments,
By Alan Stenson, CEO, Neutral Carbon Zone If you manage a facility, youโre on the front line of climate transition,
Brewers Decorator Centres are the countryโs largest independent supplier of decorating materials – supplying paint and specialist coatings, wallpaper, tools,
With more than 60 years of innovation in modular construction, Portakabin is a trusted name across the UK and Europe.
For over 60 years, TC Facilities Management (TCFM) has been delivering reliable, flexible, and high-quality soft facilities management (FM) services
CIBSE’sย Measuring Performance and Facilities Managementย conference (19 June, the Congress Centre, London) programmeย is now fully available, addressing the real challenges facilities
Managing multiple properties, emergency repairs, and varied supplier contracts makes financial control complex for facilities management teams. Soldo empowers you
Equity Energies is a UK-based energy consultancy and part of FTSE-100 listed DCC Plc. We are changing the way organisations approach
In an era defined by rising energy costs, sustainability mandates, and increasingly complex operations, energy strategy has become a critical
Ever wondered how the Ancient Romans were able to build aqueducts, grand bath houses and more? Curious about how the
At Diamond Facilities Support, weโre transforming how businesses experience maintenance and facilities management through technology, led and operating via direct
In todayโs business landscape, integrating sustainability into a supply chain is not only an ever-increasing commercial requirement, itโs also a
What is Insite? Insite is a compact, self-installed device that integrates with your Building Management System to reduce energy costs.