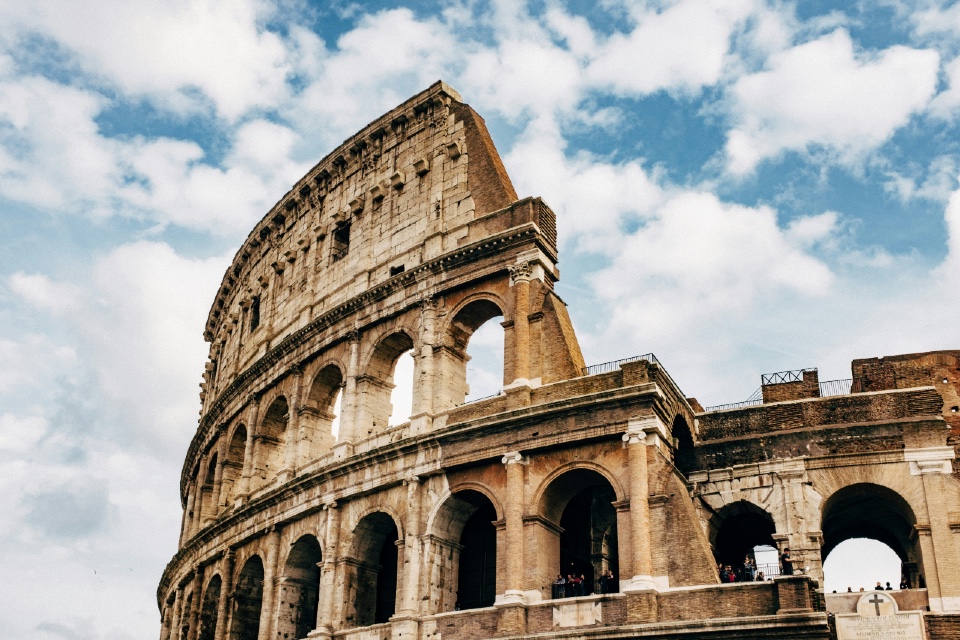
Waterproofing Through History: From ancient techniques to modern innovations
Ever wondered how the Ancient Romans were able to build aqueducts, grand bath houses and more? Curious about how the
Ever wondered how the Ancient Romans were able to build aqueducts, grand bath houses and more? Curious about how the
By Water Plus With the spotlight on energy costs and increasing focus on what organisations are doing to reduce impacts
By Kingspan During the Covid-19 Pandemic, where physical access to premises has hit an all-time low, we have all adapted
By Metro Rod Covid-19 has placed significant pressure on most industries within the UK, in a variety of different ways.
By Zip Water The COVID-19 pandemic has changed the world in incomprehensible ways. What is clear is as we emerge
With employers searching to create COVID-secure workplaces for staff to return to work safely, Zip Water have created the HydroTap
Kelly Potter, Marketing Associate, Transcendent Corporation Water is perhaps one of the most precious natural resources. With rapid urbanization, the
FreeFlow Liquid consists of ten strains of aerobic and facultative bacteria that are able to digest organic matter, such as