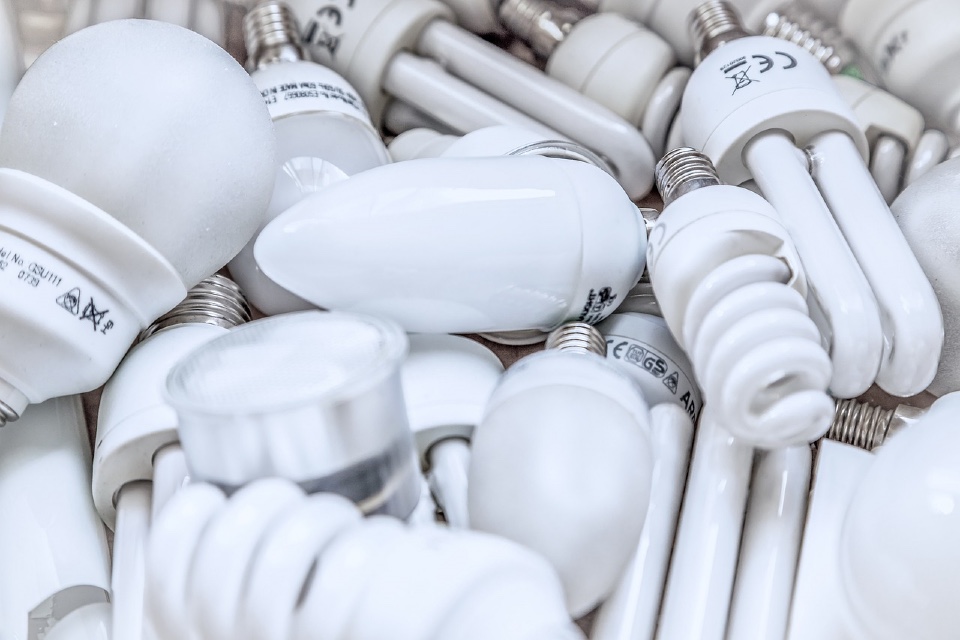
Understanding Waste Management Laws: A primer for UK-based organisations
In the UK, the responsibility of waste management doesn’t end once you’ve disposed of your waste. Comprehensive legal frameworks exist
In the UK, the responsibility of waste management doesn’t end once you’ve disposed of your waste. Comprehensive legal frameworks exist
Unprecedented pressure on supply chains has led to food buyers in the UK’s biggest organisations reporting a 60% increase in
Extended producer responsibility (EPR) schemes – key elements of the circular economy – tend to perform better when there is
If you company produces or stored hazardous waste, then it is your company’s responsibility to ensure it is stored and
The Institute of Workplace and Facilities Management (IWFM) has analysed the contents of the the government’s recently unveiled waste and
Kelly Potter, Marketing Associate, Transcendent Corporation Water is perhaps one of the most precious natural resources. With rapid urbanization, the
Cloud-based business process management company Promapp has extended its feature functionality with the launch of Lean Tagging, ensuring that organisations
We have become used to the idea of recycling. We do it at home, and more businesses are recognising the