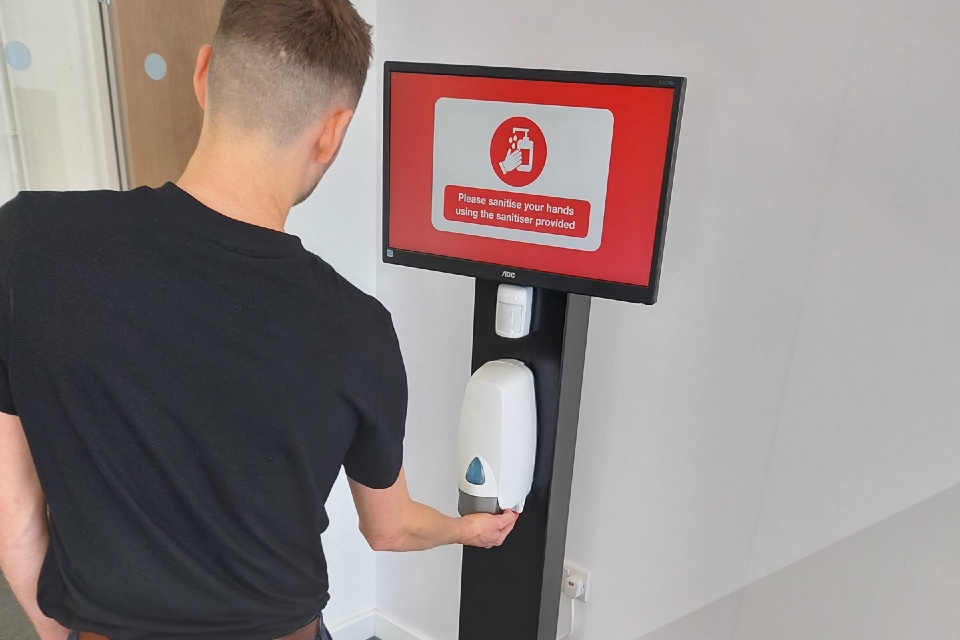
Do your employees feel safe at your premises?
By Fireco The impact of the virus on society Since the beginning of the pandemic, scientists from all over the
By Fireco The impact of the virus on society Since the beginning of the pandemic, scientists from all over the
All businesses that employ staff will be familiar with Personal Protective Equipment (PPE). Last year, the PPE Directive 89/686/EEC was