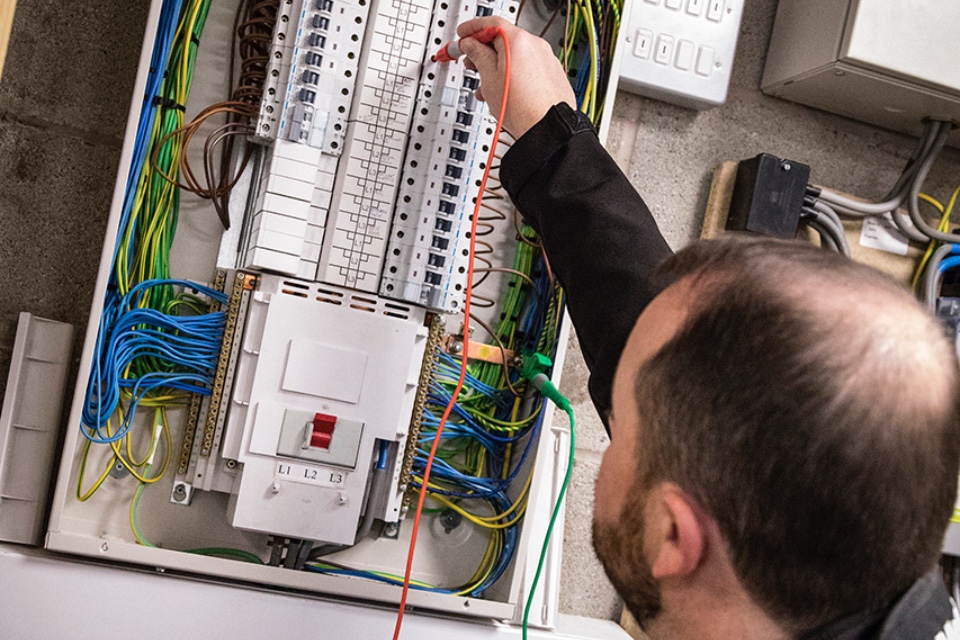
The legal changes in electrical testing every landlord needs to know about
Changes in regulation relating to electrical testing could catch out commercial and private landlords and land them with large fines,
Changes in regulation relating to electrical testing could catch out commercial and private landlords and land them with large fines,
Businesses run the risk of legal cases and thousands of pounds worth of fines for neglecting their fixed wire testing,
Businesses run the risk of legal cases and thousands of pounds worth of fines for neglecting their fixed wire testing,
phs Compliance has launched a new range of testing bundles to help businesses cut the cost of their electrical and
With many businesses now settled into a hybrid working structure, employers are being reminded of their legal obligation to ensure
The countdown to Christmas has begun and, with most festivities cancelled last year, many workplaces will be looking forward to
In the latest instalment of our FM industry executive interview series we spoke to Dan Lee (picture above, far right),
Businesses are being reminded of their legal obligation to ensure electrical equipment is safe to use at all times, even
phs Compliance is one of the UK’s leading providers of workplace compliance and building engineering services, offering everything businesses need
“Electrical testing is something that every single business has to do, regardless of current restrictions, but there is a lot
By phs Compliance Building refurbishment present risks, especially when it comes to electrical systems. Regular electrical testing is a vital